梯形螺纹主轴的表面优化 – 摩擦学分析与应用
梯形螺纹主轴是重载的理想选择,通常用于起重系统。作为生产工程和机床研究所(IFW)与博诺曼齿轮技术公司(Bornemann Gewindetechnik)合作项目的一部分,研究人员对螺纹漩涡进行了改良,以优化螺纹主轴的摩擦学特性。使用旋压微结构可将摩擦损失降低 25.5%,并显著减少粘合剂磨损。
导言
生产起重系统中常用的长螺纹主轴有多种制造工艺,包括搓丝和螺纹旋削[1]。在设计梯形螺纹主轴等标准化机器元件的制造工艺时,并未考虑其应用特性和使用寿命[2]。
在设计受滑动摩擦的表面时,必须考虑摩擦状态–边界摩擦、混合摩擦和流体摩擦–这些摩擦状态可通过 Stribeck 曲线进行分类 [3]。在流体动力状态下,力通过润滑油膜传递,摩擦力由润滑油的内部摩擦力产生 [3-5]。这与接触面积、润滑油粘度和润滑膜厚度的剪切率成正比。在混合摩擦的情况下,润滑膜在某些点会被单个粗糙度峰打断,从而导致载荷传递 [4]。特别是在低滑动速度下,这对建立和维持流体动力润滑条件不利[6]。
两个三元素之间的直接接触会增加能量消耗[7]。微结构可通过各种机制产生有利影响。例如,微结构可作为润滑剂储库[8],当润滑剂流过微结构时,润滑油膜的局部隆起可导致轴承压力增加[9]。流体动力压力可在确定的微结构中积聚。气蚀效应[4]和轴承压力在连续微结构中的积聚在这里都起了作用[10, 11]。这些研究表明,由于高负荷滑动接触,梯形螺纹主轴的表面形貌具有通过微结构减少摩擦的巨大潜力。可通过平面粗加工或激光打标等制造工艺诱导微结构,以减少滑动接触中的摩擦损失 [10,12]。 旋切作为一种制造工艺为工艺集成微结构提供了巨大的潜力,因为它比螺纹铣削等工艺的生产率要高得多 [1,13]。迄今为止,通过旋切实现表面结构化的研究仅作为一种附加的结构化工艺进行,而不是作为表面结构的工艺集成功能化[14]。有多种方法可将微结构制造作为单独的制造工艺 [12,15],但由于需要额外的工艺步骤,这些方法需要很高的集成度。Denkena 等人在一项研究中表明,通过微结构加工,暴露在高热机械负荷下的表面(如气缸套)的摩擦学特性得到了改善[12]。作为一种加工生产方法,旋压工艺由于在螺纹侧面形成了表面结构,因此具有功能化的特殊潜力(图 1)。
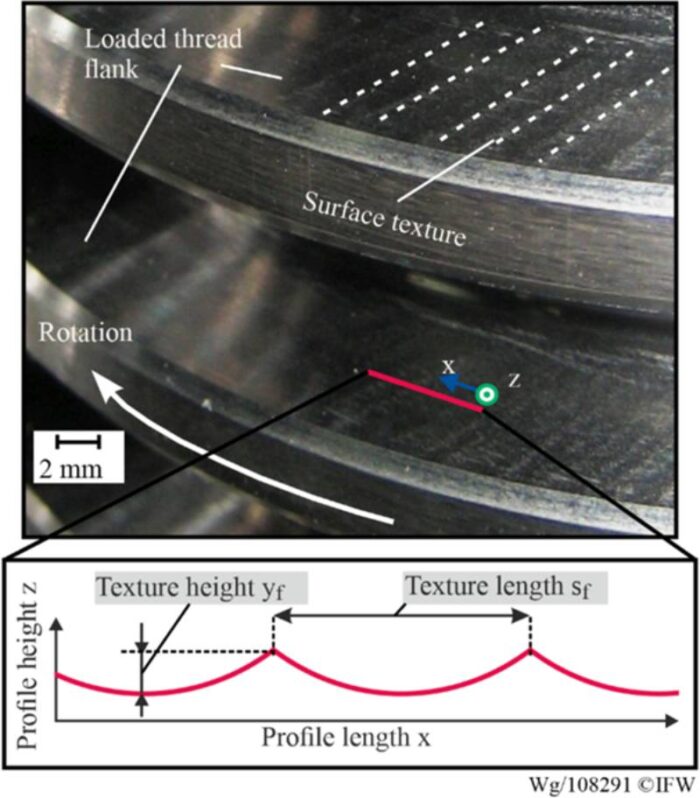
在滑动摩擦中使用金属摩擦片的一个具体挑战是,在润滑不足或过载的情况下会发生粘附。这可能导致硬度较低的摩擦副发生粘着磨损,并将材料转移到滑动接触中硬度较高的摩擦副上 [7,17]。表面形貌和滑动接触中的实际接触面积对前面提到的润滑不足导致的粘附风险起着决定性作用 [7、16、17]。两个摩擦元件之间的直接接触是粘附的基本前提,并由微接触的总数来定义。
在承受高表面压力的滑动接触中,润滑油膜厚度会减小,从而导致从混合摩擦转向边界摩擦,并伴随着摩擦系数的增大[3]。Denkena 等人的研究也表明,浅深度表面结构会导致摩擦系数降低,并转向固体和流体摩擦共存的混合摩擦状态 [12]。对于滑动摩擦中的钢青铜三元件,2-5 μm 的表面结构深度对降低摩擦特别有利 [16]。润滑不足或相对速度较低时可能出现的另一种现象是粘滑效应。这将导致三元组在短时间内相互粘连,然后再次发生滑动运动 [18]。由于缺乏润滑剂,粘滑效应的频繁发生会导致粘合剂磨损加剧,从而导致部件的早期失效 [19]。
微结构对高负荷下梯形螺纹主轴负载螺纹侧面的影响尚未得到研究,但通过减少摩擦损失提高效率的潜力巨大。此外,目前还不了解微结构对主轴-螺母系统磨损的影响。因此,本文旨在填补这一空白,研究螺纹旋转产生的表面结构在实际条件下对重型起重设备中高负载梯形螺纹主轴摩擦学行为的影响。这项研究将采用专门开发的镟屑工艺,以实现工艺集成微结构。作为研究的一部分,将介绍不同的表面结构,并评估它们对减少整个系统摩擦的影响,以及它们在表面上保留润滑剂的能力,从而防止主轴上的粘附沉积物和螺母上的粘附磨损。
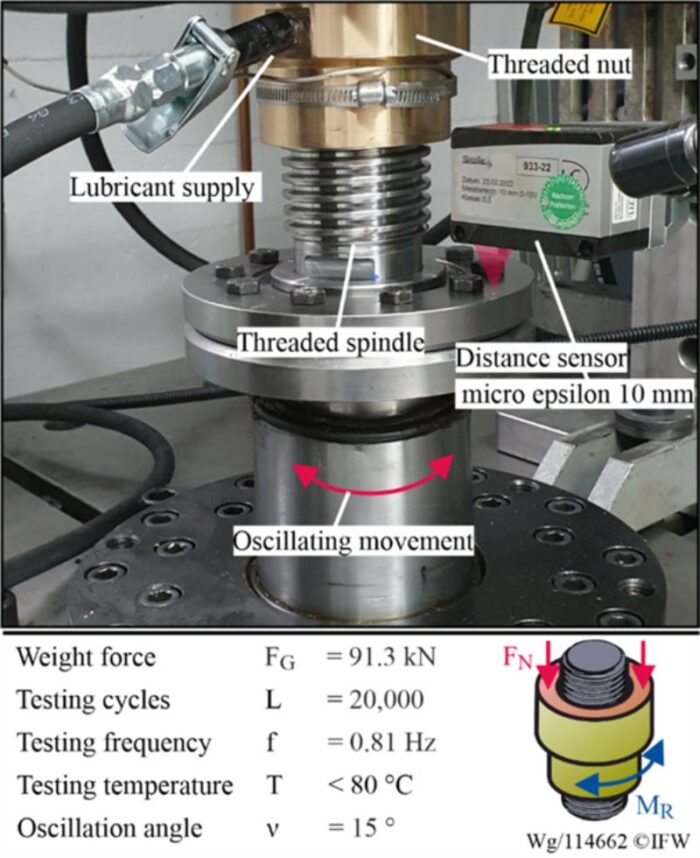
微结构对高负荷下梯形螺纹主轴负载螺纹侧面的影响尚未得到研究,但通过减少摩擦损失提高效率的潜力巨大。此外,目前还不了解微结构对主轴-螺母系统磨损的影响。因此,本文旨在填补这一空白,研究螺纹旋转产生的表面结构在实际条件下对重型起重设备中高负载梯形螺纹主轴摩擦学行为的影响。这项研究将采用专门开发的镟屑工艺,以实现工艺集成微结构。作为研究的一部分,将介绍不同的表面结构,并评估它们对减少整个系统摩擦的影响,以及它们在表面上保留润滑剂的能力,从而防止主轴上的粘附沉积物和螺母上的粘附磨损。
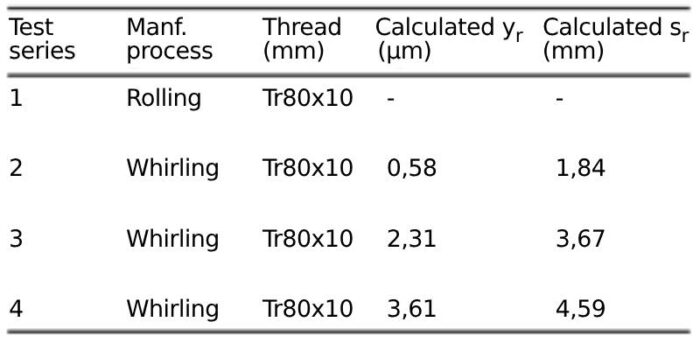
实验装置
摩擦学测试
图 2 所示的试验台用于研究螺纹侧面的表面形貌对摩擦学行为的影响。带有 Tr80×10 mm 螺纹的测试主轴以 f = 0.81 Hz 的频率在 ν = 15° 的角度上摆动。负载变化的旋转对应于螺纹主轴 0.42 mm 的平移距离。在这种设置下,螺纹主轴在升降过程中承受的重力为 FG = 91.3 kN。这相当于表面压力 p = 5.0 N/mm²,属于重型起重系统中梯形螺杆驱动装置的最大负载范围。该应用选择了螺纹螺母材料 G-CuSn 7 ZnPb。使用的润滑剂是 DGM HTF 940 润滑脂,它特别适用于滑动轴承应用。试验序列中的润滑以一个月的维护间隔为基础。该间隔相当于每 167 个循环润滑一次主轴-螺母组件。测试台由 Sincotec 安装,该公司也是力传感器 Interface 125 kN 和扭矩传感器 SincoTec 1200 Nm 的制造商。
对表面的磨损状况进行了分析,以确定不同表面形貌及其相应表面结构的摩擦特性。为此,用切割磨床将主轴切开。在 20,000 次载荷循环下,通过实验测算出分析螺纹主轴的使用寿命为 10 年。
为了研究其摩擦学特性,我们制备了四种螺纹主轴,并将不同的工艺参数与使用旋压工艺的轧制主轴进行了比较(表 1)。对于旋压螺纹主轴,选择工艺参数的方式是使螺纹受载螺纹侧面的表面结构高度之间达到确定的梯度。试验系列 1 包括使用连续轧制工艺制造的轧制螺纹主轴。具体的工艺参数基于鲍诺曼的经验。测试系列 2 采用符合最新技术水平的工艺参数进行旋压,作为新开发的表面结构的额外参考。
在测试系列 3 和 4 中,本研究开发的表面结构分两个阶段生产,以增加表面结构高度 yf 和表面结构长度 sf。这两个结构参数的增加会导致表面润滑剂保留量的增加。测试系列 3 显示,理论结构高度 yf = 2.31 μm,结构距离 sf = 3.67 μm。在测试系列 4 中,结构参数更为明显,yf = 3.61 μm,sf = 4.59 μm。这清楚地表明了涡流过程对结构可调整性的限制:结构高度 yf 的增加必然导致结构长度 sf 的增加。
测量表面结构
Confovis GmbH 的 Duo Vario 光学测量系统用于分析实验生成的三维表面形貌。使用共焦白光显微镜记录表面形貌。共聚焦测量使用尼康 20×/0.45-NA 物镜进行。侧向测量分辨率为 0.20 微米,用于分析侧翼表面。测量区域的宽度为 2.26 毫米,长度为 8.71 毫米,分辨率为 0.28 微米。实验中产生的螺纹主轴在正交测量位置上与螺纹侧面对齐。
表面地形的应用和特征
以下结果显示了螺纹侧面的表面形貌如何通过旋压工艺进行特殊调整,以及它与搓丝工艺的有限形貌有何不同。图 3 显示了滚压梯形螺纹主轴的螺纹侧面与旋压螺纹侧面的表面形貌对比。
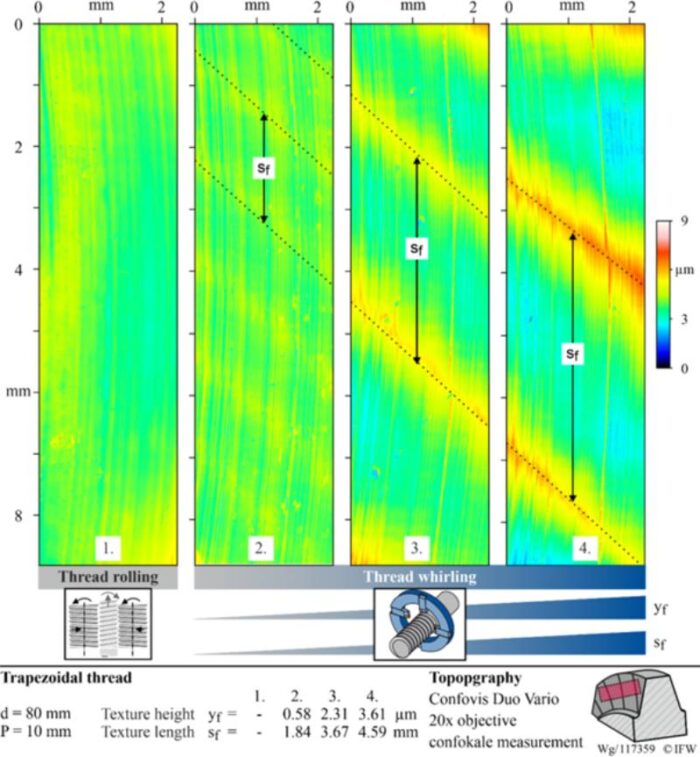
测试系列 1 的表面形貌显示,在搓丝过程中没有产生表面纹理。与测试系列 1 相比,测试系列 2 的旋压螺纹主轴表面形貌没有明显差异,也没有可识别的表面纹理。通过特别调整搓丝工艺,在测试系列 3 和 4 中可以产生明显的表面纹理。在这些测试系列中,纹理高度 yf 和纹理长度 sf 相继增加,以产生峰值比例较低的表面纹理,从而最大限度地减少三元组表面之间的直接固体接触。表面纹理峰值之间的距离越大,就越有可能在粗糙度轮廓的谷中保留润滑剂。
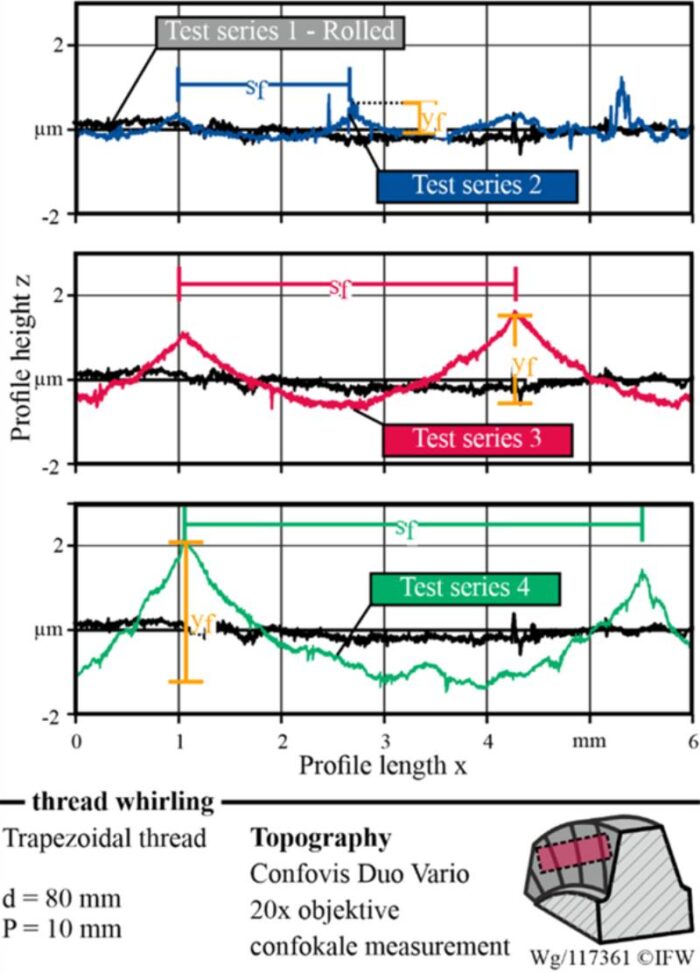
由于在加工过程中出现了随机粗糙度效应,对技术表面产生了四度形状偏差,因此叠加了试验系列 2 中不明显的表面纹理。由于这种叠加,纹理参数难以确定,纹理高度 yf = 0.82 μm,纹理长度 sf = 1.63 mm。实际上,由于表面纹理较少,试验系列 2 与轧制样品没有区别。旋切过程中的随机粗糙度效应主要由旋切工具切削刃上的粗糙度造成,也称为崩边。这在加工过程中会在新生成的表面上形成负模[20]。测试系列 3 和 4 的地形图显示了由崩角产生的特征性重复沟槽。如果纹理高度 yf 小于旋切刀具切削刃的粗糙度 Rz,纹理就会叠加,旋切过程的特征纹理就不会出现。这可以从螺纹侧面的粗糙度轮廓中看出(图 4)。
此外,由于从表面形貌中减去了数学上近似的螺纹形状,测量结果也会失真,因此测量范围边缘的纹理高度略低(图 3 和图 4)。
摩擦学评估
利用第 2.2 节所述的试验装置,分析了用于重型起重系统的梯形丝杠主轴中漩涡状表面纹理对丝杠和螺母摩擦系统的影响。在梯形螺杆的设计中,为简化起见,通常假定摩擦系数为常数。然而,摩擦系数不能被视为一种材料属性,因为它受到摩擦系统所有组件的影响。为了说明表面形貌对该系统的影响,所有影响变量都保持不变。在测试系列中,只有制造过程引起的表面纹理会发生变化。
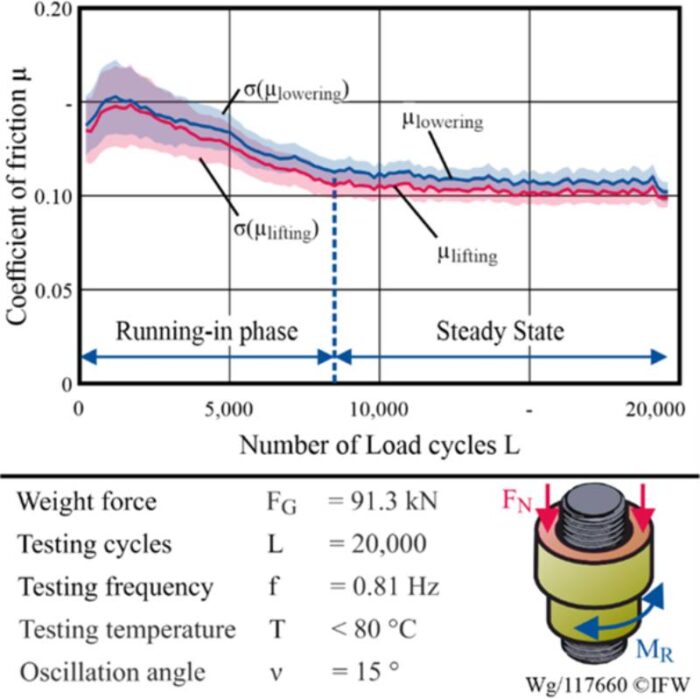
摩擦系数调查
在重型提升系统中,移动螺杆通常垂直布置,因此在提升和下降运动过程中,受力螺纹侧面都会受力。斜面上的摩擦力可用于计算梯形螺纹的摩擦系数[21]。法向力 FN 可以通过重量力 FG 计算得出,摩擦力 FR 则可以通过旋转运动所需的摩擦扭矩利用几何关系计算得出。这导致在提升过程中所需的摩擦力矩大大增加。由于摩擦力矩是在测试装置中测量的,而重力 FG 被设定为一个恒定值,因此可以根据这些变量计算出摩擦系数 μ。考虑到力分量的不同方向,可以分别确定提升和下降的摩擦系数 μ。试验系列 1 中轧制主轴这两种运动的摩擦系数示例过程如图 5 所示。考虑到力的方向不同,两种运动的摩擦系数曲线相似。尽管提升所需的驱动扭矩较大,但可以看到梯形螺纹主轴在 20 000 次载荷循环中的摩擦系数特性。 这两种运动的平均摩擦系数在试验开始时显著增加,在大约 2000 次循环时达到最大值,然后在大约 8000 次循环时降至恒定水平。这种行为被称为磨合阶段,描述了整个试验过程中摩擦系数的总体变化,具体取决于摩擦学系统[22]。小角度范围内的摆动运动模拟了载荷变化过程中短距离的升降。在负载变化过程中产生的速度曲线包括加速阶段、恒速阶段和减速阶段,每个阶段分别用于提升和降低。低速时会产生粘滑效应,尤其是在方向逆转的转折点。这种效应表现为表面的短暂粘滞,然后是摩擦元件的突然滑动。这种运动会导致振动,反映在摩擦系数的较大偏差上 [19]。从图 5 中可以观察到,在最初的 5000 次负载循环中,摩擦系数的偏差较大。
所分析的梯形螺纹 Tr80×10mm 在经过约 8000 次载荷循环后达到了恒定的摩擦系数。在磨合阶段,测试轧制梯形螺纹时摩擦系数最初会增大,这也与摩擦系数的高偏差有关。最高的摩擦系数与最大的偏差有关,这表明粘滑效应的发生率增加,可能导致粘合剂磨损加剧。由于这两种运动的摩擦系数曲线相似,下文只考虑用力较大的提升运动。
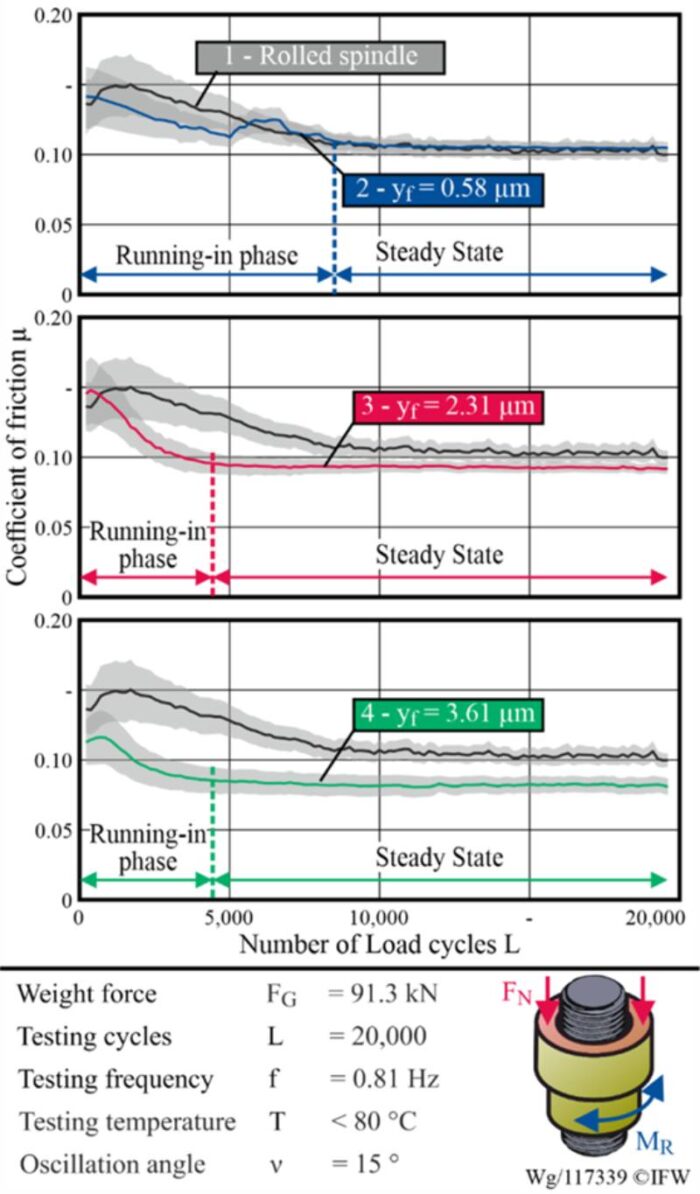
图 3 所示的表面摩擦系数曲线存在明显差异。虽然测试系列 1 和 2 的制造工艺(搓丝和旋丝)不同,但两个样品的表面形貌相似,几乎没有表面纹理(图 3)。这种相似性也反映在摩擦系数曲线上(图 6)。试验系列 1 的摩擦系数出现了明显的最大值,而试验系列 2 在整个试验过程中都没有出现最大值。不过,在这两项试验中,经过相似次数的负载循环(L ≈ 8000)后,摩擦系数都达到了一个恒定水平。
在整个试验过程中,两次试验的平均摩擦系数 μm 也是相似的。旋压式和滚压式螺纹主轴都有一个磨合阶段,这导致摩擦系数非常稳定,在 μ = 0.1 的水平上几乎没有偏差。在纹理高度为 yf = 2.31 μm 的试验系列 3 中,磨合阶段明显缩短,大约在 4500 次负载循环后完成。与滚压(μm = 0.115)和无纹理旋压螺纹侧面(μm = 0.112)相比,测试系列 3 的平均摩擦系数μm 可降至 μm = 0.098,相当于摩擦系数降低了 14.6%。在测试系列 4(yf = 3.61 μm)中可以看到更明显的减少,其中引入的表面纹理既减少了约 44% 的窜动行为,又将摩擦系数永久性地降低到 μm = 0.085 的较低水平,与滚压螺纹主轴相比,相当于减少了 25.5%。不过,在所述摩擦学系统中,使用这种螺纹不可能完全减少磨合阶段。
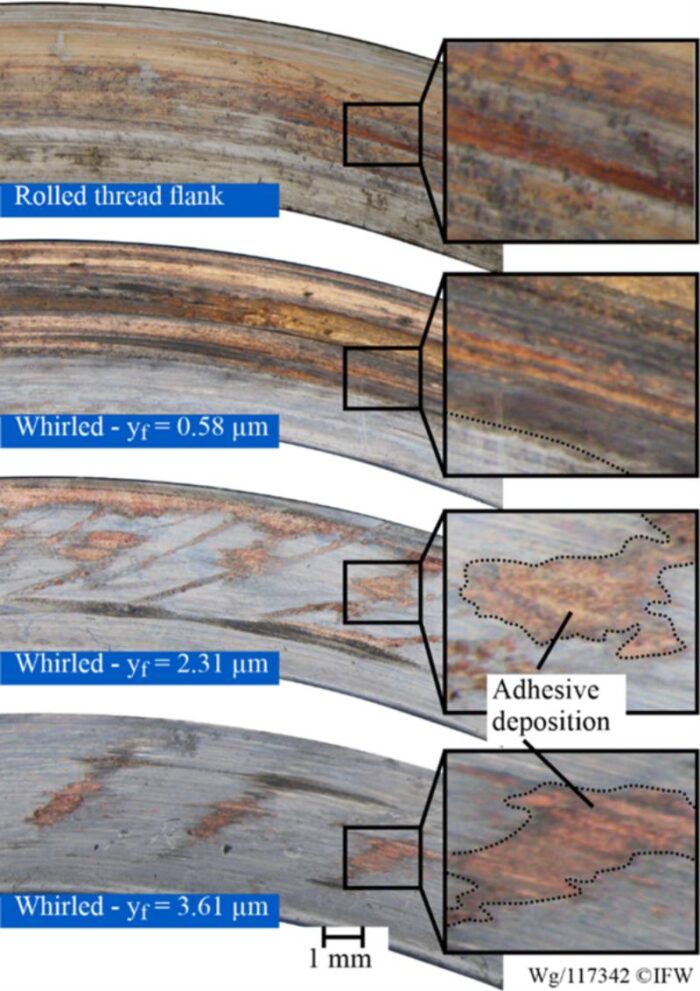
粘合剂磨损分析
主轴和螺母接触时产生的磨损对梯形丝杠传动装置的使用寿命起着决定性作用。为了确定导向螺杆的磨损机理,我们在 FG = 91.3 kN 的重力和定期润滑的情况下,经过 20,000 次负载循环后,对负载螺纹侧面的表面进行了检测(图 7)。测试结束后,测试系列显示出明显不同的磨损模式,这取决于加载螺纹侧面的表面结构。测试系列 1 和 2 在加载螺纹侧面没有表面结构的情况下进行测试,结果显示螺纹主轴的加载螺纹侧面有明显的粘附沉积物。这是由于螺母材料受到严重侵蚀或粘着磨损造成的。从测试系列 3 到测试系列 4,随着结构高度的增加,粘着磨损程度明显降低(图 7)。
为了确定已加载螺纹侧面被粘附沉积物覆盖的比例,对显微镜图像进行了彩色分析,以量化由材料 G-CuSn 7 ZnPb 中的铜含量引起的主要为红色的沉积物。对加载螺纹侧面面积相关附着率的评估显示,滚压梯形螺纹主轴的附着率最高,为 36.3%(图 8)。测试系列 2(旋压螺纹侧面)显示覆盖面积偏差最大,为 27.4%,标准偏差为 13.1%。在实验模拟的使用寿命结束后,该测试系列表面的某些区域出现了高达 45.4 % 的粘附残留物。测试系列 4 的磨损模式表明,yf = 3.61 μm 的结构高度降低了粘附磨损的比例,并将其限制在粗糙度峰值区域(图 8a)。 带旋涡螺纹侧面的测试系列 2 的表面覆盖面积偏差最大,为 27.4%,标准偏差为 13.1%。在实验模拟的使用寿命结束后,该测试系列表面的某些区域有高达 45.4 % 的粘合剂残留。测试系列 4 的磨损模式表明,纹理高度为 yf= 3.61μm 时,粘合剂磨损的比例和粗糙度峰值区域的峰值都会降低(图 8a)。
由于摩擦学接触中的滑动速度低、表面压力大,摩擦学系统中的摩擦被区分为固态摩擦和混合摩擦。
在测试系列 3 中,螺纹侧面的粘合剂磨损从 36.3% 降至 13.6%,在测试系列 4 中,与滚压螺纹主轴相比,旋压侧面的粘合剂磨损进一步降至 10.1%。 在表面纹理明显的粗糙度峰值之间没有发生粘合。根据粘合剂涂层的特性,可以推测存在从边界摩擦状态到混合摩擦状态的转变。根据 Wang 等人的研究,较少的粗糙度峰值,或者在这种情况下只有表面纹理的峰值,会导致摩擦系数的降低[4]。在这些区域,旋转过程中形成的原始表面保持不变。
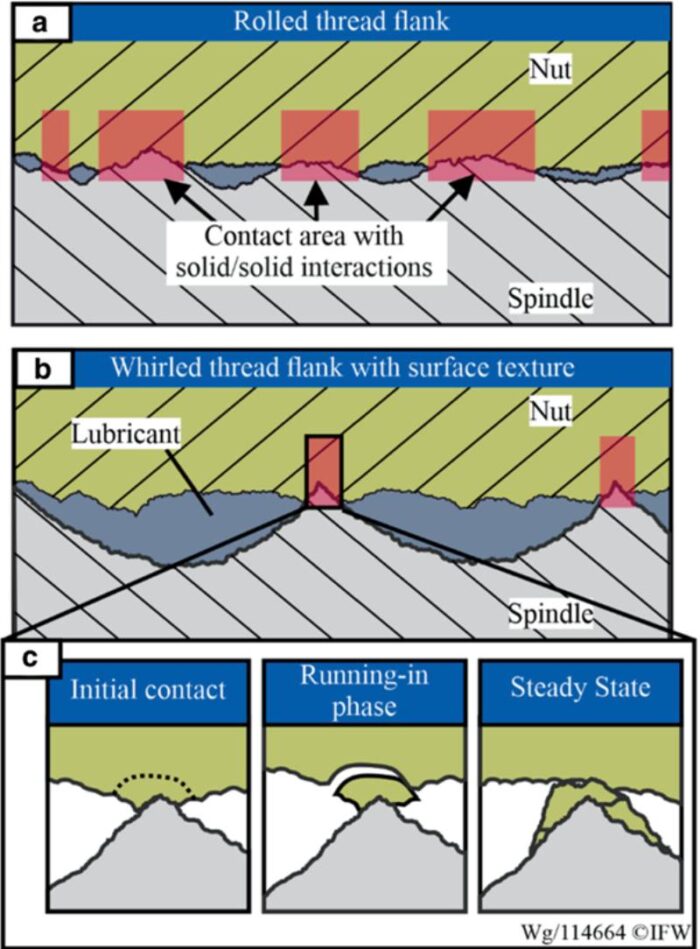
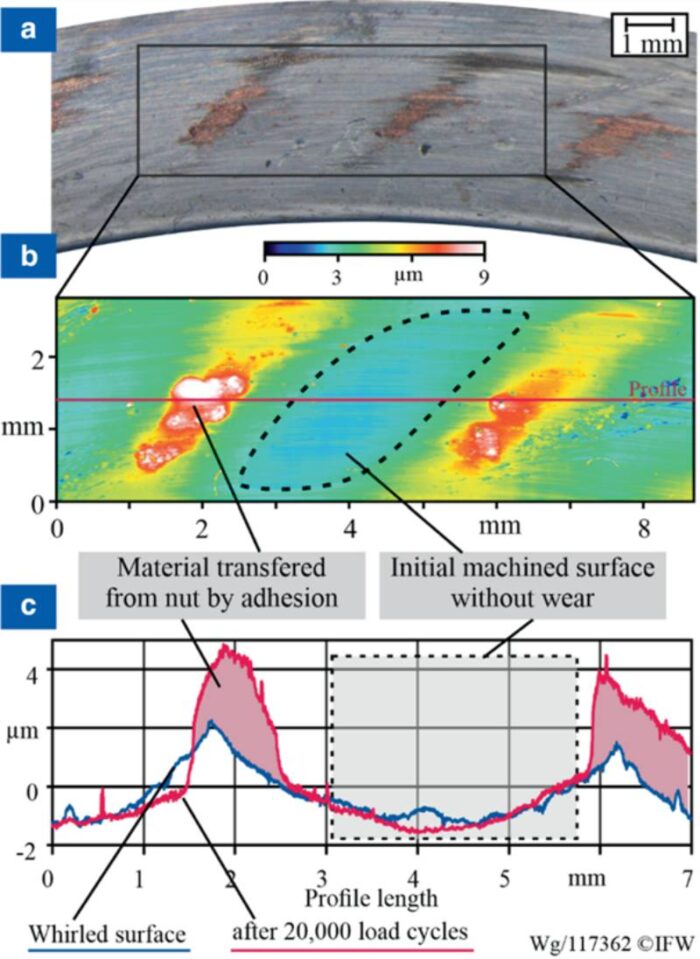
如文献[10]所述,微量成分的连续排列也有利于形成一层薄薄的润滑膜。由于整个接触面的固体摩擦减少,螺纹主轴运动所需的摩擦扭矩降低。润滑油可以储存在表面结构明显的区域,从而增加润滑油膜厚度,产生流体摩擦,防止表面之间直接接触。三元素粗糙度峰之间的直接接触可能是造成粘着磨损的原因之一 [19]。
由于表面纹理更加明显(图 9b),固态摩擦的比例与非结构化表面形貌(图 9a)相比有所下降。螺纹侧面更明显的表面纹理可以吸收更多的润滑剂。
当由不同金属制成的摩擦元件接触时,材料会从内聚力较低的摩擦体(在本例中为螺母)转移到内聚力较高的基体(在本例中为螺纹主轴)上 [3]。摩擦接触中的额外润滑剂会降低接触粗糙度峰值的数量。图 9c 中的示意图显示了加载螺纹侧面粘附沉积物的形成。螺纹螺母接触面的逐渐加载导致沉积在加载螺纹侧面接触粗糙度峰上的颗粒脱离。这些颗粒越来越多地在加载螺纹侧面的接触面上形成一层(图 10),阻止螺杆和螺母材料之间的直接接触。这一过程一直持续到达到静止状态,螺母表面边界层不再有材料转移到装载螺纹侧面为止。当接触粗糙度峰值被粘合剂沉积物覆盖时,这一过程会影响磨合行为并转变为静止状态。这会影响摩擦系数。图 10 显示,沉积物高约 2 μm,加载螺纹侧面的初始表面没有磨损。
结论与展望
作为这项研究的一部分,我们使用旋转方法调整了三种不同的表面形貌,并检验了它们在梯形螺纹主轴上的摩擦学特性。除了测量摩擦系数外,还分析了螺纹主轴负载螺纹侧面的磨损模式,并对粘附沉积物进行了量化。
事实证明,与滚压螺纹主轴相比,重型起重系统中使用的螺纹主轴负载螺纹侧面的表面结构具有相当高的附加值。旋压工艺可以生产出更多种类的表面结构,使摩擦系数降低 25.5%。由于主轴和螺母之间的摩擦接触对效率有很大影响,因此如果考虑到起重系统的特定轴承,摩擦系数的降低会导致整个系统的能耗成比例降低。此外,可以证明的是,螺纹主轴的原始表面在旋转过程中形成纹理,即使在实验模拟的 10 年使用寿命之后,仍然基本完好无损。这表明,主轴和螺母粗糙度峰值直接接触的固态摩擦比例可以降低。采用上述表面纹理后,螺纹侧面的粘着磨损在测试系列 4 中降低到 10.1%,而采用滚压螺纹主轴时则为 36.3%。
尽管在测试中模拟了螺纹主轴的整个 10 年使用寿命,但螺纹螺母的使用寿命并未显示。虽然只有主轴的一部分暴露在摩擦接触中,但螺母的内螺纹却承受着持续的载荷,因此暴露在摩擦相互作用中的时间要长得多。未来的研究可以更多地关注摩擦系统的这一方面,特别是考虑到测量螺母磨损的难度。具有明显表面结构的螺纹主轴的另一个积极作用可能是减少反摩擦体(此处为螺母)的磨损。
鸣谢
作者衷心感谢联邦经济和气候保护部(BMWK)的资助以及项目合作伙伴 Bornemann Gewindetechnik GmbH & Co. KG 的建设性密切合作。
促销活动
这些研究由联邦经济和气候保护部(BMWK)资助,是中央创新促进计划的一部分。
作者的贡献
B. Denkena 与 B. Bergmann 一起审阅并编辑了手稿。C. Wege 提出了这项工作的概念,进行了实验,分析了数据并撰写了手稿。M. von Soden 和 H. Gereke-Bornemann 制作了工具并提供了实验装置。
促销活动
开放获取资金由项目 DEAL 提供和组织。
利益冲突
B. Denkena、B. Bergmann、C. Wege、M. von Soden 和 H. Gereke-Bornemann 声明不存在利益冲突。
开放存取
本文采用知识共享署名 4.0 国际许可协议进行许可,该协议允许以任何媒介或格式使用、共享、改编、分发和复制本文,但必须适当注明原作者和来源,提供知识共享许可协议的链接,并对任何变更予以确认。本文中包含的来自第三方的图片或其他材料均包含在文章的 “知识共享 ”许可中,除非在材料出处中另有说明。如果材料未包含在文章的知识共享许可协议中,而您打算使用的材料不在法律允许范围内或超出了允许范围,您必须直接从权利持有人处获得许可。如需查看该许可的副本,请访问 http://creativecommons.org/licenses/by/4.0/。
出版商说明
施普林格-自然》对有关出版地图中的地理标志和机构隶属关系的法律纠纷保持中立。