搓丝得分与搓丝得分的比较
摩擦接触约占全球总能耗的 12%。其中,20%用于克服摩擦,3%用于维修磨损部件或更换磨损相关故障的设备[1]。其中一个例子就是用于维修火车或卡车的重型起重设备。鲍诺曼齿轮技术公司专门从事此类复杂或高应力螺纹部件的制造。这家家族企业与汉诺威莱布尼茨大学生产工程和机床研究所(IFW)合作,利用螺纹旋压工艺对梯形螺纹的摩擦学优化进行了研究。该工艺尤其适用于长螺纹部件。Bornemann Gewindetechnik 公司采用最先进的生产技术,生产长达 12 米的螺杆型材。
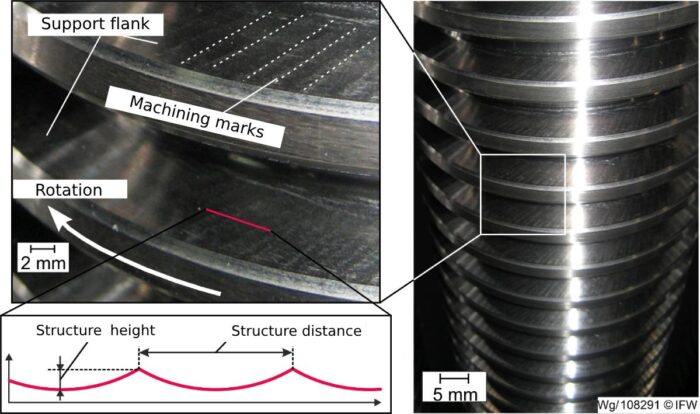
旋压螺纹主轴具有与加工相关的表面微结构,可提供润滑剂保持量。与传统的轧制主轴相比,这减少了旋压螺纹主轴的摩擦,延长了使用寿命。作为 “TopThread ”项目的一部分,研究人员正在研究加工过程与减少摩擦效果之间的确切关系。
我们正在研究螺纹旋切产生的微结构对重型起重系统中高负载梯形螺纹主轴摩擦学特性的影响。为此,正在分析专门为加工一体化微结构而开发的镟屑工艺。
本文将说明如何利用旋压工艺对表面形貌进行专门调整,这与搓丝工艺相比具有显著优势。图 2 显示了滚压梯形螺纹主轴的螺纹侧面与旋压螺纹侧面的表面形貌对比。
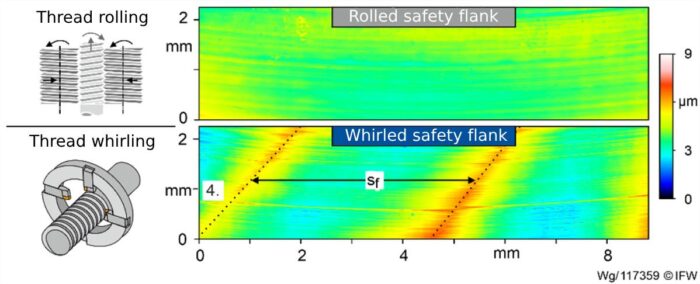
与滚压螺纹主轴相比,通过专门调整旋压工艺,可以生产出更明显的结构。结构参数结构高度 “yf ”和结构间距 “sf ”用于描述表面结构(图 1)。为了优化摩擦学,旋压工艺用于制造峰值比例较小的结构,从而最大限度地减少摩擦副表面之间的直接固体接触。结构峰之间的距离越大,润滑剂就越有可能储存在粗糙度轮廓的凹谷中。
摩擦学特性表征
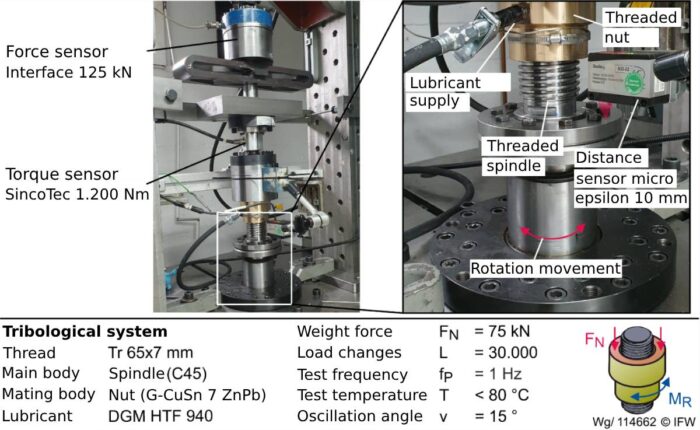
图 3 所示的试验台用于研究螺纹侧面的表面形貌对摩擦学特性的影响。螺纹 Tr 为 80 x 10 mm 的测试主轴以 f = 0.81 Hz 的频率摆动,摆动角度为 v = 15°。负载变化的旋转相当于螺纹平移 s = 0.42 mm。在这种设置下,螺纹主轴在升降过程中承受的重力为 FG = 91.3 kN。这相当于表面压力 p = 5.0 N/mm2,属于重型起重系统中梯形螺杆驱动装置(TGT)的最大负载范围。为此,选择了 G-CuSn 7 ZnPb 螺纹螺母材料和 DGM HTF 940 润滑剂。试验序列中的润滑相当于一个月的维护间隔。因此,主轴-螺母组件的润滑间隔为每 167 个周期。试验台由 SincoTec 安装。SincoTec 还是力传感器 Interface 125 kN 和扭矩传感器 SincoTec 1,200 Nm 的制造商。
对侧面的磨损状况进行了分析,以确定不同表面形貌和表面结构的摩擦特性。为此,项目参与者使用切割磨床对主轴进行了切割。在 20,000 次载荷循环的情况下,通过实验测算出了所分析螺纹主轴的十年使用寿命。对于旋压螺纹主轴,在选择工艺操作变量时考虑到了螺纹承重侧面微结构高度之间的渐变。这些工艺参数是根据鲍诺曼的经验确定的。此外,还分析了使用连续工艺轧制的轧制螺纹主轴。
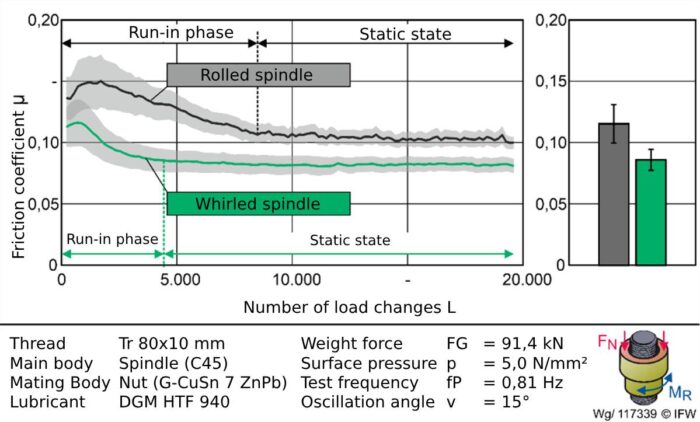
表面结构对摩擦系数的影响
由于摆动运动的角度距离很小,因此可以在大量的载荷循环中对升降进行分析。通过这种方法,可以通过实验测绘出螺纹主轴的整个使用寿命。图 4 显示了梯形螺杆驱动提升运动的摩擦系数变化过程。这里比较了滚动导螺杆和旋转导螺杆的摩擦系数。在载荷变化过程中产生的速度曲线包括加速阶段、恒速阶段和减速阶段–在每种情况下均为提升和下降阶段。在低速时会产生粘滑效应,在方向逆转时尤为明显。这种效应表现为表面的短暂粘滞,随后摩擦副突然滑动。这种运动会导致振动,反映在摩擦系数的更大波动上[2]。平均摩擦系数在试验开始时急剧上升,在大约 2 000 个负载循环后达到最大值,然后在大约 8 000 个负载循环后下降到恒定水平。这种行为被称为磨合阶段,描述了摩擦系数在试验过程中的总体变化,具体取决于各自的摩擦学系统[3]。
旋转的梯形螺纹主轴采用了新的表面结构,其摩擦学特性得到了显著改善。与滚压螺纹主轴相比,摩擦系数降低了 25.5%。在所述的摩擦学系统中,使用这种螺纹不可能完全减少磨合阶段。
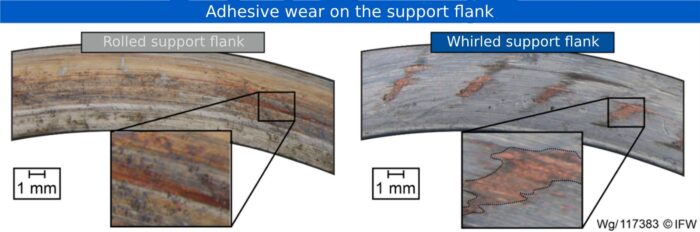
表面结构对磨损的影响
两个摩擦副接触时产生的磨损对梯形螺纹主轴的使用寿命至关重要。为了确定螺纹主轴的磨损机制,在定期供应润滑剂的情况下,对轴承侧面的表面进行了 20,000 次负载循环试验,然后对轴承侧面的磨损模式进行了分析(图 5)。测试结果表明,轴承侧面的表面结构不同,磨损模式也明显不同。轴承侧面无表面结构的滚压螺纹主轴在螺纹主轴轴承侧面有明显的粘着沉积物,这是由于螺母材料的大量去除或粘着磨损造成的。随着结构高度的增加,粘着磨损的面积也明显减少(图 5)。
由于摩擦学接触的滑动速度低、表面压力高,摩擦学系统中的摩擦可分为固态摩擦和混合摩擦。由于表面结构明显(图 6,右),与无结构的表面形貌(图 6,左)相比,微接触的数量可以减少。这使得表面结构导致的固态摩擦比例降低。螺纹侧面更明显的表面结构能够吸收更多的润滑剂。使用表面结构后,螺纹侧面的粘着磨损降低到 10.1%,而使用滚压螺纹主轴时则为 36.3%。
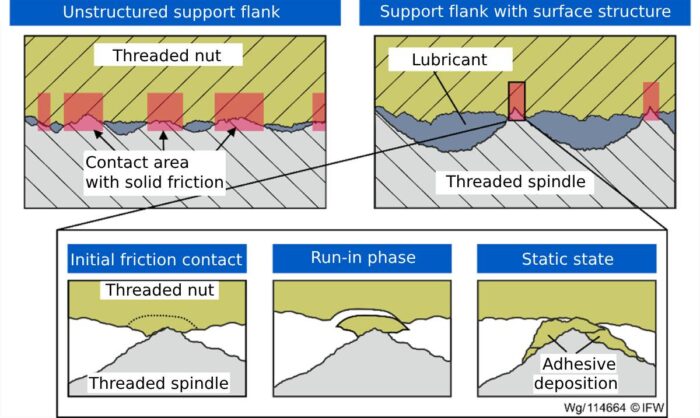
当由不同金属制成的摩擦副接触时,材料会从内聚力较弱的粘合摩擦体(在本例中为螺母)转移到内聚力较强的粘合基体(在本例中为螺纹主轴)[4]。摩擦接触中的额外润滑剂会降低接触粗糙度峰值的数量。螺纹螺母接触面上的渐进载荷导致沉积在轴承侧面接触粗糙度峰上的颗粒脱落。这些颗粒逐渐在轴承侧面的接触区域形成一层,阻止了主轴和螺母材料之间的直接接触。这一过程一直持续到达到静止状态,轴承侧面不再有沉积物为止。这一过程决定了磨合行为,一旦接触粗糙度峰被附着沉积物覆盖,磨合行为就会转变为静态。这种状态也会影响摩擦系数。在提升运动过程中,初始表面不会受到任何磨损。
前景和利用方案
在与滚压螺纹主轴的竞争中,用于重型起重系统的螺纹主轴轴承侧面的表面结构已被证明具有相当高的附加值。旋压工艺可用于制造更多种类的表面结构。此外,实验还表明,螺纹主轴表面的磨损非常小,这意味着轴承侧面的表面结构在经过 10 年的实验模拟使用寿命后仍能基本保留。图 7 显示了微结构轴承侧面在梯形螺纹主轴设计和制造中的三大潜力。
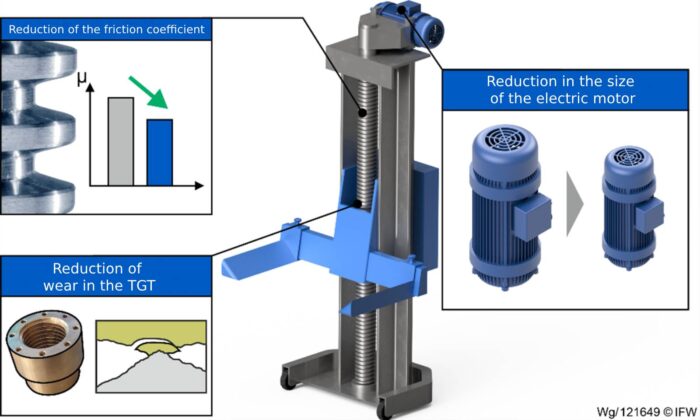
通过对螺纹表面结构的调整,可以将摩擦系数降低 25.5%。以重型起重系统为例,由于主轴和螺母之间的摩擦接触对效率起着决定性作用,因此考虑到起重系统的相应轴承,摩擦系数的降低会导致能耗成比例地减少。
另一个方面是减少螺纹螺母的磨损。在这些研究中,螺纹螺母的磨损只能根据轴承侧面的粘合剂沉积物进行间接分析。由于轴承侧面的粘附沉积物减少到约 10%,可以推断摩擦副之间的微接触减少,因此螺纹螺母的磨损也减少。从轴承侧面附着物的减少可以得出结论,螺纹螺母的整体磨损也会减少。这可以降低维护成本,延长整个梯形螺杆传动装置的使用寿命。
微结构导螺杆轴承侧面的第三个也是决定性的优势来自于驱动电机的设计。通过将摩擦系数降低 25%,可以在设计中考虑降低摩擦扭矩。
这样就可以选择较小尺寸的电机,从而降低整个系统的功耗,大大降低整个提升系统的投资成本。不过,在这方面必须减少磨合期,并在整个使用寿命期间保证恒定的摩擦系数。
通过进一步研究,可以根据螺纹几何形状优化表面结构。目前,项目合作伙伴正在为生成这些经过专门调整的表面结构的过程申请专利。
这样就能更有针对性地解决个别摩擦系统的问题。未来研究和开发的另一个方面是修改螺纹螺母的表面形貌,以便对磨合行为进行专门补偿。摩擦系数的不断降低将使设计驱动电机时进一步缩小尺寸成为可能。这些问题将在未来与鲍诺曼风电技术公司(Bornemann Gewindetechnik)和国际风能联合会(IFW)共同规划的研究项目中得到进一步解决。
鸣谢
作者感谢 ZIM 资助 “TopGewinde – 通过摩擦学优化表面形貌,利用旋转工艺延长螺杆传动装置的使用寿命 ”项目。
他们还要感谢 Bornemann Gewindetechnik 制造商 Hans Bornemann 和 Moritz von Soden 在研究项目中的出色合作。
文学
[1] Holmberg K, Erdemir A (2017 Influence of tribology on global energy consumption, costs and emissions. Friction 5, 263-284 (2017)
[2] Haessing D A, Friedland B (1990) On the Modeling and Simulation of Friction. American Control Conference, San Diego.
[3] Denkena B, Böß V, Nespor D, Gilge P, Hohenstein S, Seume J (2015): Prediction of the 3D Surface Topography after Ball End Milling and its Influence on Aerodynamics, 15th CIRP Conference on Modelling of Machining Operations, Procedia CIRP 31, S. 221 227
[4] Buckley D H (1981) Surface Effects in Adhesion, Friction, Wear and Lubrication. S. 456. Elsevier, Amsterdam.
联系我们
Christian Wege, M. Eng.
汉诺威莱布尼茨大学生产工程与机床研究所
电话: +49 (0) 511 762 4606
wege@ifw.uni-hannover.de