飞行:使用可转位硬质合金刀片旋削螺纹时的表面效果与磨削相当
螺纹制造工艺最初可分为三大类: 初级成型。成型、切割。一次成型主要用于通过注塑成型制造塑料螺钉和螺母。
承受高应力的螺纹通常采用热成型或冷成型。其中最重要的工序无疑是外螺纹的搓丝。因为只有达到最佳疲劳强度,才能实现高产量。
由于需要达到很高的精度,加工制造工艺起着特殊的作用。大多数运动螺纹,如梯形主轴。滚珠丝杠和测量主轴等对精度要求较高的产品。都是通过机械加工制造的。
说到机械加工生产方法,众所周知有多种制造工艺,例如车螺纹、追螺纹、切螺纹、攻螺纹、铣螺纹、旋螺纹和磨螺纹。生产中最终使用哪种工艺取决于几个因素: 工件总数、表面质量、螺纹轮廓、公差、材料、生产设备、购置成本、运行成本(如工具)、工件产量、系统易受故障影响的程度。
车螺纹、切螺纹、攻丝和追螺纹等长切削加工工艺的优点已广为人知,但其缺点也相当严重,尤其是长切削材料在加工区域容易出现故障。
以三种短切削工艺为例,主要介绍了鲜为人知的螺纹旋切工艺。
在螺纹铣削中,首先要区分两种工艺:短螺纹铣削和长螺纹铣削。短内螺纹和外螺纹通常是尖形螺纹,是用圆柱形螺纹铣刀加工出来的,铣刀沿其长度方向具有整个螺纹轮廓。铣刀上相邻的螺纹轮廓没有间距。轮廓间距与要生产的螺纹螺距完全一致;轮廓齿经过浮雕研磨。主要使用高速钢铣刀,因此一把铣刀只能加工出相同螺距的螺纹。大多数情况下使用反向旋转。
螺纹铣削时的高切削力
其优点是生产时间短,切屑呈逗号状且较短。缺点是切削力大,对精度和表面质量有负面影响,尤其是长度较长时。此外,铣刀直径在修磨过程中也会发生变化,成本非常高,因此必须对调整路径或路径半径进行修正,例如在加工中心上。
由于每个螺纹螺距都需要一把铣刀,因此这种方法主要用于大规模生产。切屑形成时产生的表面几何形状也不理想,尤其是在螺纹底部。长螺纹铣削用于加工长螺纹。盘形轮廓铣刀通常由高速钢制成,带有浮雕磨齿,如果轮廓宽度较大,则配有可转位刀片。铣削轴根据螺纹螺距或螺距角倾斜。对于需要一次切削完成的较大轮廓宽度或较大前角,需要在刀具上进行轮廓修正。
同步铣削是高质量螺纹的首选。长螺纹的简单加工,通常只需一次切削就能达到整个螺纹深度,这一点尤为有利。由此产生的短切屑也很容易清除。端面铣削对于挤出机螺杆区等大轮廓宽度也很有利。由于长度长、直径小、轮廓宽度大,预计螺距偏差会更大,表面质量会更差。与铣削类似,在磨削过程中,旋转工具进行切削运动。磨粒的棱角将工件上的逗号形切屑去除。淬硬工件(如带有异形盘的滚珠丝杠)通常需要磨削。这些工件通常使用其他工艺进行预成形,因此每个螺纹侧面只需去除约 0.15 毫米。全轮廓深磨也很常见,即在一次切削中去除整个轮廓。砂轮连续成型,例如使用修整金刚石滚轮。
可达到的表面质量、淬硬材料的生产和轮廓精度都是其优点。缺点当然是机器购置成本高,冷却润滑剂、切屑和氧化铝的分离复杂。
在螺纹旋转过程中有利于切屑形成
在经济的同步旋转过程中,工件(机床主轴)相对较慢的进给(nR)始终与刀环的旋转方向相同。硬质合金刀头以较高的圆周速度(转速 nw)旋转,无振动且均匀一致。
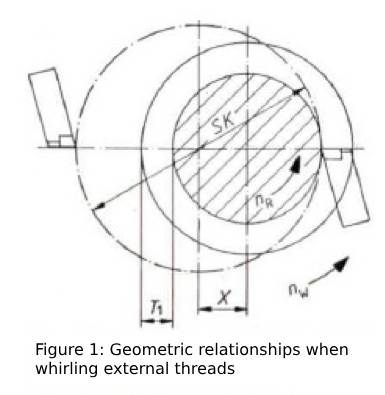
与铣削相比,这些增加值要小得多,而且与螺纹芯部有关。根据螺纹侧面角度的不同,该值在侧面仅为 ¼ Y 左右。
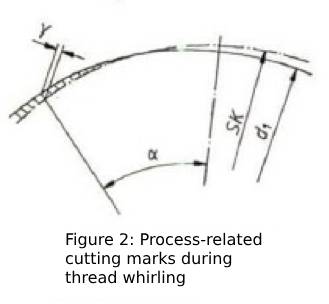
采用高切削速度和有利的包络圆切削,进给率高,切削时间短,质量上乘。结合使用方便且经济的刀具系统,可生产出高产能的精密螺纹。由于切屑呈逗号状,因此不会像车削那样因切屑过长而停机。
使用所谓的往复式旋压工艺可以生产出较长的内螺纹。旋转和摆动工具通过一个固定的导向手支撑在芯孔中。工具配备了多刃可转位刀片。
例如,在大型镗床上使用特殊的旋转装置加工重型部件的内紧固螺纹。涡轮机制造中就采用了这种工艺。对于加工中心上的较小工件,则只能通过使用适当的螺纹旋削工具进行圆周加工来加工螺纹。这些工具带有无需调整的四刃刀片。